top of page
CRAZY WOLF
Spatial thinking and communicating
Individual Project
By: Emmanuel Navas Castro
Fall 2022
​
Crazy wolf is the name of my final design for a "beautiful" machine that portraits the overall movement of a dogs mouth and eyes. First it was necessary to transmit the idea through sketches of the different perspectives/faces of the machine(isometric view) to finally build the actual machine using the 3D modelling software called Onshape.

Final product
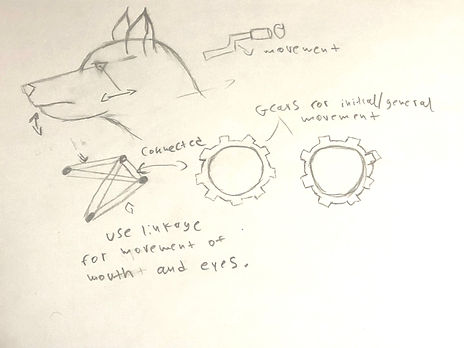
First ideation skecth
I started by ideating possible ideas for the machine. Thinking about what actions i find to be interesting, which led to wolves/canine since i find wolves to be intriguing. After having found the action that I wanted to do, it was necessary to transmit the core concept of the idea through a simple sketch
Once I had the complete idea i passed into a detailed sketch of the inner mechanism of my machine. For it i considered how to move the mouth to open and close in a vertical motion while at the same time have the eyes move in a horizontal motion by moving only one lever. For it, i used a 90 degree gear connection.

Inner mechanism sketch

Side views of inner mechanism
With the finalized idea and the sketch of the inner structure of the machine, all that was left was to test its functionality and construction in Onshape. The first thing to do was test how the machine worked before finalizing the design of the carcass and adjusting the dimensions of the machine to properly fit with the carcass.
The machine itself was done smoothly and without much complications other than learning the detailed functions of the program Onshape. The carcass, on the other hand ,turned out to be quite challenging. Since i wanted to build the 3D head of the wolf.
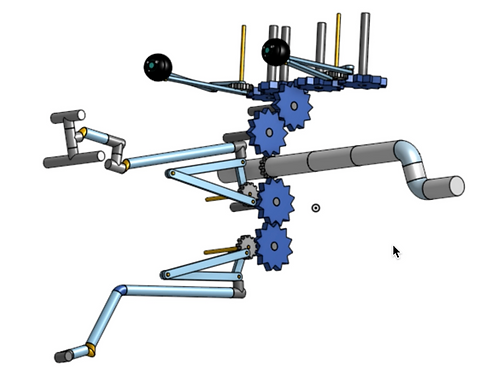
Onshape mechanism model

Onshape Carcass model
The Biggest difficulty was making the sides of the carcass so they look the same. The first solution i thought was to make both sides by hand, meaning that, just like the rest of the carcass that was built as if sculpting from a simpler and bigger shape to the final design, do both side decorations. The problem with that solution is the amount of time it requires to be done. Therefore, i thought of a simpler and faster way to address the problem. I decided to build half the carcass (cutting it through a vertical axis in the middle) and then mirror that half to complete the machine.
The only thing i would do differently on this project if i had more time would be to add more features to the machine's carcass, especially the back 'face'. Although, i am very satisfied by the final product.
The project itself was a great application of 3D modelling, thinking on the different perspectives of the machine as well as drawing them. which is an essential knowledge to transmit ideas easier and clearer. I learned how to think and see the different faces of an object and how to communicate them to others. Nonetheless, i also mastered most of the functions of Onshape since the project required an advanced knowledge of Onshape's tools.
bottom of page